The installation of Direct Digital Control (DDC) systems follows a structured process to ensure efficiency and reliability in commercial.
HVAC systems. Our installation process includes:
-
Pre-Installation Planning – We review project specifications, electrical schematics, and control diagrams to ensure proper integration with the building’s HVAC system. Coordination with general contractors and engineers is essential.
-
Mounting and Wiring – Our team installs the DDC controllers in designated control panels or enclosures, ensuring proper positioning for accessibility and ventilation. We then connect field devices (sensors, actuators, relays) to the controller using low-voltage wiring, following best practices for cable management.
-
Power and Network Configuration – Controllers are wired to power sources and connected to the BACnet or Modbus network, ensuring seamless communication with the Building Automation System (BAS).
-
Sensor & Equipment Integration – We integrate temperature, humidity, pressure, and occupancy sensors, along with actuators, dampers, and variable frequency drives (VFDs), configuring inputs and outputs as required.
-
Programming and Commissioning – Our technicians will maintenance & calibrate sensors, and test system responsiveness.
-
Final Testing and Client Handover – We perform a functional performance test (FPT), verify alarms and trend logs, and provide training for facility managers before finalizing the installation.
"Our goal is to ensure seamless automation, energy efficiency, and long-term reliability in every DDC system we install."
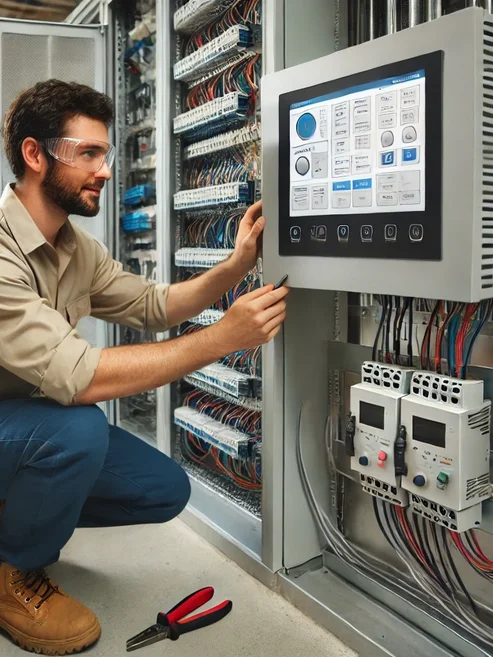
"Our company specializes in seamless Building Automation System (BAS) integration, ensuring that all HVAC components communicate efficiently for optimized performance, energy savings, and ease of operation."
Our BAS Integration Process:
- System Design & Coordination – We collaborate with general contractors, engineers, and facility managers to install a custom BAS solution tailored to the building’s HVAC infrastructure and operational needs.
-
Controller & Device Installation – Our team installs DDC controllers, sensors, actuators, and other field devices, ensuring proper wiring and connectivity for real-time data collection and control.
-
Network Communication Setup – We integrate controllers into the building’s BACnet, Modbus, or LonWorks network, ensuring interoperability with third-party equipment. Secure IP or MSTP configurations are implemented for reliable data exchange.
-
Testing & Commissioning – A comprehensive physical point-to-point check is conducted to validate sensor readings, actuator movement, and network communication. Functional performance testing (FPT) ensures system reliability before full deployment.
-
User Training & Handover – We provide hands-on training for facility personnel, ensuring they can monitor, control, and troubleshoot the system through the BAS workstation or remote access.
"Our BAS integration enhances building efficiency, reduces operational costs, and ensures long-term HVAC system performance."
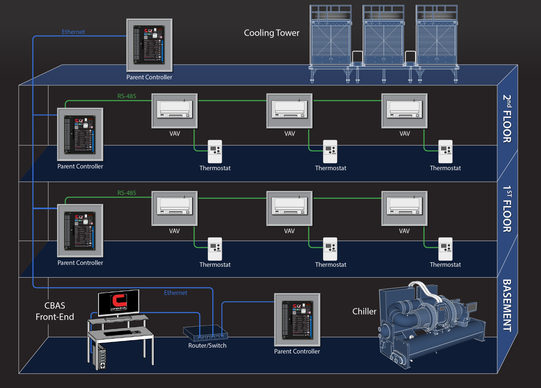
Building Automation Systems (BAS) require regular Maintenance & prompt Troubleshooting to ensure optimal performance, energy efficiency, and system reliability. This guide provides a structured approach to diagnosing issues and maintaining BAS components.
1. Common BAS Issues & Troubleshooting Steps
A. Communication Failures
-
Check network connections, IP settings, and baud rates for mismatches.
-
Restart controllers and verify firmware versions.
-
Inspect cables and terminations for loose or damaged wiring.
B. Sensor Malfunctions
-
Verify sensor placement and ensure no environmental interference.
-
Compare sensor readings with manual measurements for accuracy.
-
Calibrate or replace faulty sensors as necessary.
C. Controller & Actuator Issues
-
Confirm proper power supply to controllers and actuators.
-
Check control sequences and override settings.
-
Reset or reprogram controllers if necessary.
D. Alarm & Notification Errors
-
Review alarm logs to identify recurring faults.
-
Verify threshold settings to avoid false alarms.
-
Test alarm notifications to ensure proper escalation.
E. Preventive Maintenance Best Practices
-
Perform routine inspections of controllers, sensors, and actuators.
-
Keep firmware and software updated to the latest versions.
-
Clean and secure all network and electrical connections.
-
Conduct seasonal performance tests to optimize efficiency.
F. System Optimization & Performance Tuning
-
Analyze trend logs to identify inefficiencies or inconsistencies.
-
Optimize control loops for better energy management.
G. Documentation & Reporting
-
Maintain detailed records of troubleshooting activities and maintenance logs.
H. Support & Future Upgrades
-
Establish a regular maintenance schedule for long-term system health.
-
Plan for system expansions or integrations with new technologies.
-
Offer training for on-site personnel on troubleshooting and minor adjustments.
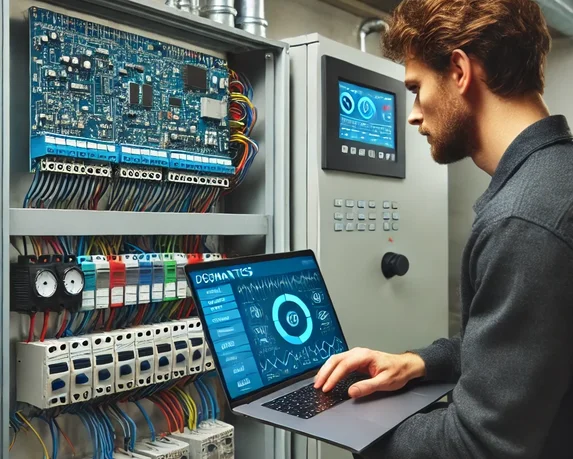
Upgrading and Retrofitting Existing Building Automation Systems (BAS)
1. Overview
Upgrading and retrofitting existing Building Automation Systems (BAS) is essential to improve energy efficiency, extend system lifespan, and integrate modern technologies. This guide provides a structured approach for evaluating, planning, and executing BAS upgrades and retrofits.
2. Assessment & Planning
-
Conduct a thorough assessment of the existing BAS, including hardware, software, and network infrastructure.
-
Identify outdated components, compatibility issues, and inefficiencies.
-
Establish upgrade goals such as energy savings, enhanced automation, or expanded system capabilities.
-
Develop a phased implementation plan to minimize disruption to building operations.
3. Hardware Upgrades
-
Replace legacy controllers with modern DDC controllers that support open protocols like BACnet and Modbus.
-
Upgrade sensors, actuators, and field devices to improve accuracy and reliability.
-
Ensure compatibility with existing HVAC, lighting, and security systems.
4. Software & Network Enhancements
- Integrate cloud-based monitoring and remote access capabilities for real-time control.
-
Optimize network infrastructure by upgrading to IP-based communication where feasible.
5. System Integration & Expansion
-
Integrate new equipment and subsystems, such as lighting controls, access control, and energy management tools.
-
Ensure seamless communication between new and existing BAS components.
-
Implement automation sequences and data analytics to optimize building performance.
6. Testing & Commissioning
-
Conduct thorough testing of all upgraded components and ensure proper integration.
-
Perform functional performance tests (FPT) to validate control sequences and energy savings.
-
Troubleshoot any interoperability issues and fine-tune system settings.
7. Training & Handover
-
Supply documentation, including updated system diagrams, programming logic, and user manuals.
-
Establish ongoing support and maintenance plans to ensure long-term system performance.
8. Future-Proofing & Scalability
-
Design upgrades with scalability in mind to accommodate future expansions.
-
Stay up to date with emerging BAS technologies and industry trends.
-
Implement predictive maintenance strategies using data analytics and AI-driven insights.